Automated Timekeeping Takes Gunnison to New Heights
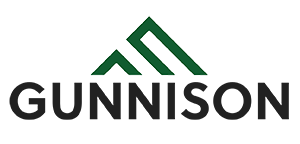
Automated Timekeeping Takes Gunnison to New Heights
TimeControl plays pivotal role as a trusted data source to support vegetation management leader’s digital transformation
Established in 2020 to bring more than 120 years of tree trimming expertise together under one unified brand, Gunnison Co. is on a mission to be the safest, most
innovative and effective vegetation management provider in the U.S.
Each work day, the Atlanta, GA-based company’s agile crews are high in the air, using the latest equipment to remove trees along roadways, clear rights-of-way and power lines, and maintain large-scale properties on behalf of utilities, municipalities, businesses and homeowners. Now the back office supporting those workers is learning to be just as nimble in the ‘cloud.’
As part of a multi-pronged digital transformation journey aimed at digitizing, automating and streamlining administrative processes across the company’s six divisions, Gunnison recently transitioned to the NetSuite cloud-based ERP. In order to automate billing and give decision-makers better visibility into labor and equipment activity on a per project basis, the company needed a consistent and reliable way to collect hours, for both labor and equipment.
Not only was timekeeping of their information spread out in various siloes across the company, but at the time, the only way to gather it into one place for reporting purposes was to create a new spreadsheet, a process that often required manual entry with no guarantee that everyone would be working from the same version.
“We had a lot of divisions collecting time their own way on custom spreadsheets, which worked fine, but resulted in inconsistencies and errors, and some folks were still on paper,” said Gunnison CIO Marc Picardo. “Our goal is to use data to drive decisions but in order to make that happen, we have to be able to standardize and trust our timekeeping information.”
Flexibility to also track equipment
After considering several options and an extensive search online, Gunnison found its answer in TimeControl® Industrial Online, a modern enterprise timesheet system from HMS Software that supports crew-based timekeeping on a task-by-task, project-by-project basis.
One of the biggest selling points, said Gunnison Solutions Architect James McGreger, is the flexibility within the software that allowed the team to meet their integration needs with other business systems for reporting and analysis purposes. An essential feature in TimeControl Industrial that wasn’t available in other timekeeping solutions they found was the ability to track not only labor but also monitor equipment usage.
“We don’t treat equipment as a material cost applied to a project. We track equipment by the hour and that means we need to be able to record equipment hours the same way we do people hours,” McGreger explained. “We also needed the ability for a single person to approve and enter time on behalf of an entire crew.”
Supported by HMS Software deployment specialists, the Gunnison IT team started to prototype a timekeeping solution in February 2023 and five months later the system was fully deployed in the field to track time for 1,100 crew members and 2,000 pieces of equipment.
“Working with Gunnison was a pleasure,” explained HMS Software’s Director of Technical Services Stephen Eyton-Jones. “Not all clients have such an articulate appreciation of what processes they are trying to improve and how they want to be supported throughout the deployment. In the case of Gunnison, the questions, the requests and the internal understanding of their own systems and processes that were implicated in the deployment were crystal clear.”
“I can’t say enough good things about the HMS technical team and their support in helping us to do our implementation and track down issues,” said McGreger. “It was crucial to our ability to achieve our goals in the aggressive timeline we set.”
Each week, general foremen use the TimeControl web interface to enter time for their crews in a crew timesheet, applying the software’s charge functionality to track different activities and rates. For example, mechanical crews, bucket crews and climbing crews are each treated as separate activities within the program, and they can also apply four rate types: straight time, overtime, double time and premium time.
API access supports user-specific customization
“We needed to be consistent in the way time was entered so that we could make better business decisions and have visibility,” said McGreger, adding that general foremen have the option of using one timesheet per crew or managing multiple crews on one timesheet.
“We were able to meet all of our deadlines and train users consistently so that everybody is entering data the same way, regardless of which division they’re in or which project they’re working on,” he said.
McGreger credits the smooth rollout to the unique API (Application Programming Interface) access in TimeControl that supports and simplifies software integrations, allowing Gunnison to automatically generate timesheets according to user preferences as opposed to having users create their own timesheets each week. Employee information is automatically imported from the human resources information system (HRIS) and equipment information is imported from the fleet management system.
“We did everything we could to minimize the time users need to spend on clicking and entering data versus doing what they’re great at, which is trimming trees,” he said.
“We were able to help Gunnison during the deployment with the TimeControl API. Even though Gunnison’s programmers were doing the integration work, they were able to identify several TimeControl end-points we could add or improve that let them get the access they needed for a complete integration with multiple external systems,” explained TimeControl Senior Developer Carl Duguay. “Gunnison’s requests were very specific and their technical people clearly understood what they needed. That made the process very straightforward and they seemed happy with how quickly the integrations then came together.”
Automated timekeeping delivers immediate benefit
TimeControl is now a key component of Gunnison’s digital transformation journey, Picardo emphasized.
For the first time, they have a trusted, auditable data source about exactly how many pieces of equipment and how many employees worked on a project, when and for how long. The information easily feeds into NetSuite to drive costing at the project level and into Power BI for data visualization and reporting. A cloud integration platform, Boomi, is used behind the scenes to help push and pull the data between multiple systems.
Picardo said the benefit of automated timekeeping in a cloud environment was immediate from an accounting perspective. Not only is the team able to use time entered into TimeControl for cost accounting, but they’re also able to recognize revenue on fixed price projects.
“We’re doing analytics at the project level and then presenting that data to our operations team so they have a better look at who is on what project,” said Picardo. “It all stems from having one source of time data entry that multiple systems can then utilize as a trusted source.”
TimeControl offers internal validation tools that the client manages and can be useful in helping to keep the data accurate, such as preventing a general foreman from recording more than 40 hours of straight time per week, per employee. Gunnison has added an automated rule that means it’s impossible to record time against a piece of equipment or employee who isn’t part of their crew, or against a project that’s no longer in the system. This makes a huge impact on data quality. When potential errors are caught at the time of entry, the entire system’s data becomes more reliable.
A trusted source for clean, consistent data
Feedback from Gunnison’s TimeControl users is extremely positive, with some general foremen reporting that the ability to track time at a granular level is helping them to manage their crews better in the field. Timekeeping data from TimeControl is also being imported into Gunnison’s project management software to help schedulers advance projects in a timely fashion.
The company is now considering TimeControl as the system of record for payroll timekeeping, as well as a trusted data source for the fleet management system to help with managing repairs. The company’s safety team has also expressed interest in implementing TimeControl to manage their hours.
“As part of our digital transformation, we’ve really strived to define where a particular piece of information is going to live and for timekeeping data, it’s TimeControl,” said McGreger. “We’re taking the manual manipulation of spreadsheets out of the mix and laying the groundwork to run reports and make decisions we could only dream of before because our data was so scattered.”
“HMS Software has been a great partner for us through this transformation,” added Picardo. “When we identify enhancements, we’d like to make, they’re on it and they understand exactly what we need and why. In many cases, the changes we need are a simple configuration adjustment or something data related, and it’s done almost instantly. In some cases, we’re looking for something more technical, and even then, the response from the TimeControl team is extremely timely. For us, that nimbleness has been fantastic.”
You can download this TimeControl Case Study at: gunnison_case_study.pdf
For more information about TimeControl, please contact: www.timecontrol.com/contact or info@hms.ca.
For more information about Gunnison, please see gunnisoncompany.com.